Lifting Inspections in South Wales
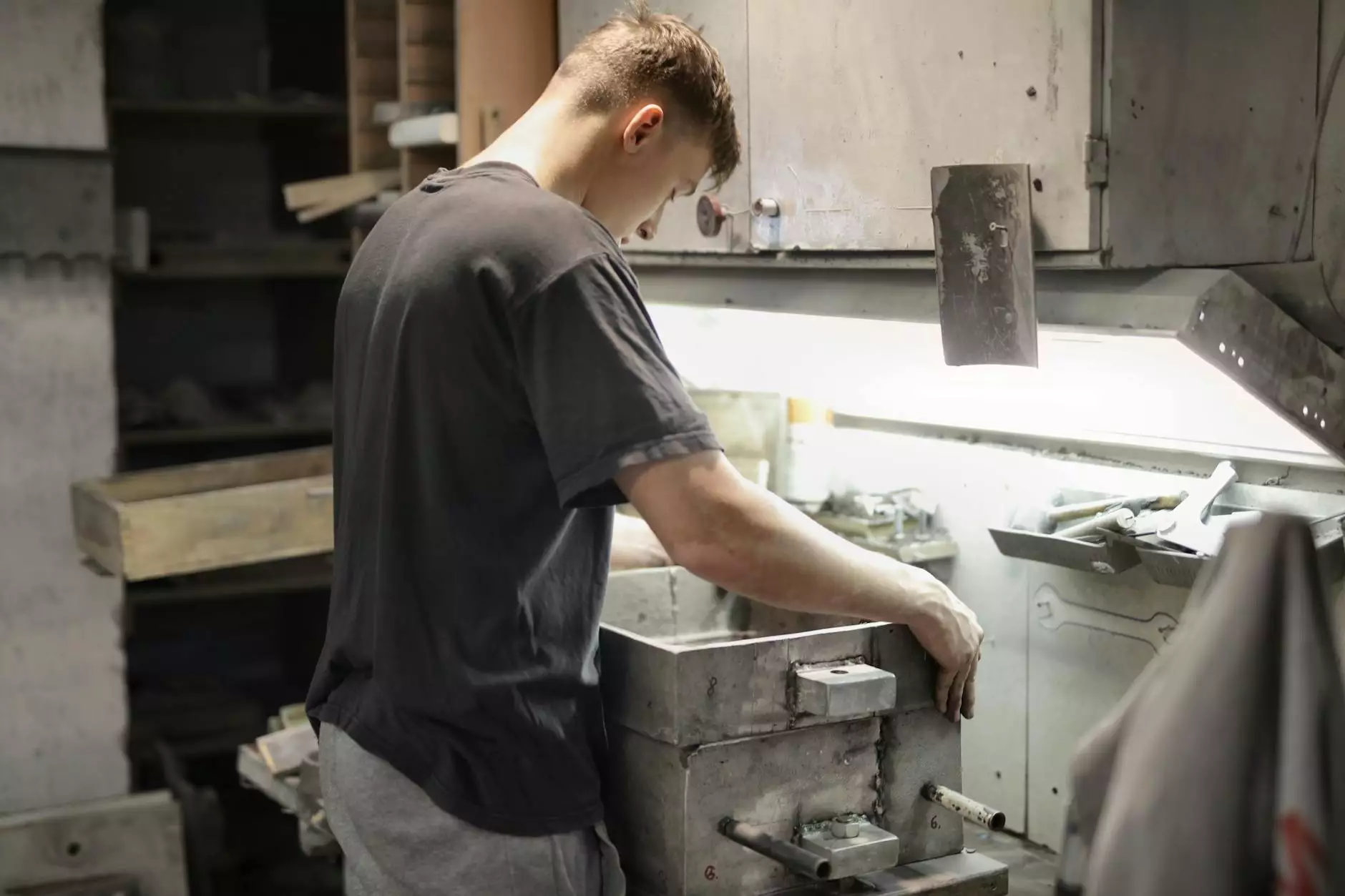
In today’s competitive business environment, maintaining safety and compliance is crucial, especially in industries that rely heavily on machinery and lifting equipment. This comprehensive guide covers everything you need to know about lifting inspections in South Wales, including regulations, benefits, and how to choose the right inspection services.
The Importance of Lifting Inspections
Lifting equipment is pivotal in many sectors, from construction to manufacturing. Regular inspections are not just a legal requirement but a fundamental aspect of maintaining a safe workplace. Here are some of the key reasons why lifting inspections are critical:
- Compliance with Regulations: South Wales, like the rest of the UK, has stringent safety regulations that govern the use of lifting equipment. Adhering to these rules helps avoid legal penalties.
- Preventing Accidents: Regular inspections identify potential faults before they cause accidents, ensuring the safety of employees and reducing the risk of costly downtimes.
- Enhancing Equipment Longevity: Routine checks and maintenance extend the life of lifting equipment, leading to higher returns on investment.
- Improving Operational Efficiency: Well-maintained equipment operates more effectively, leading to increased productivity and smoother operations.
Understanding the Regulations for Lifting Inspections
In South Wales, as part of the UK, lifting operations are governed by various regulations. The most prominent among these is the Lifting Operations and Lifting Equipment Regulations (LOLER) 1998. This legislation mandates that all lifting equipment be:
- Suitable for the intended use
- In a safe condition
- Regularly inspected by a qualified person
- Properly maintained
Employers must ensure that lifting equipment is inspected at specified intervals. For lifting equipment, inspections must occur at least every 6 months, while lifting accessories should be inspected every 12 months. Failure to comply can result in severe penalties and increased risks of accidents.
Types of Lifting Equipment Subject to Inspections
Various types of lifting equipment require inspections, including but not limited to:
- Cranes: Mobile, overhead, and hoist cranes need to be thoroughly checked.
- Forklifts: Regular inspections are essential for ensuring operational safety.
- Winches and Hoists: These require inspections to verify their load-bearing capabilities.
- Lifting Accessories: Slings, chains, and hooks should all undergo routine checks.
Choosing a Lifting Inspection Service in South Wales
Selecting the right inspection service is crucial for ensuring compliance and safety. Here are several factors to consider when choosing an inspection provider:
- Accreditation: Ensure the company holds relevant certifications and accreditations, such as those from the Health and Safety Executive (HSE).
- Experience: Look for a firm with a proven track record in the industry and specific experience with the types of lifting equipment you use.
- Range of Services: Opt for a provider that offers comprehensive services, including risk assessments, maintenance, and emergency repair services.
- Customer Service: Good communication and support are essential, especially when dealing with urgent inspections or repairs.
Benefits of Utilizing Professional Lifting Inspection Services
Engaging professional lifting inspection services comes with numerous advantages:
- Expert Knowledge: Professionals possess the technical expertise to identify issues that an untrained eye may overlook.
- Time-Saving: Outsourcing inspections allows you to focus on your core business activities while ensuring safety compliance.
- Peace of Mind: Knowing that a qualified expert is handling your inspections instills confidence in your workplace safety.
Case Studies: Success Stories from South Wales
Numerous businesses across South Wales have benefitted from rigorous lifting inspections. Here are two noteworthy examples:
Case Study 1: Construction Firm A
A prominent construction firm conducted regular lifting inspections, ensuring compliance with LOLER. This proactive approach significantly reduced workplace accidents and improved employee morale, as workers felt safer on site.
Case Study 2: Manufacturing Company B
A well-established manufacturing company utilized a reliable lifting inspection service that not only inspected their equipment but also provided maintenance recommendations. This service led to a 30% increase in machinery uptime and a notable reduction in repair costs.
How Safe Plant UK Can Help You with Lifting Inspections
At Safe Plant UK, we specialize in providing top-notch lifting inspection services tailored to businesses in South Wales. Our certified inspectors have extensive knowledge and experience, ensuring that your equipment is safe, compliant, and operationally efficient. Our services include:
- Comprehensive Inspections: We perform thorough checks on all types of lifting equipment.
- Safety Reports: Detailed reports outlining compliance status, recommendations, and any required actions.
- Ongoing Support: Our team is readily available for questions, emergencies, and follow-up inspections.
Partner with Safe Plant UK to ensure the safety and reliability of your lifting equipment. Our expert team is dedicated to providing unparalleled service and support to businesses of all sizes in South Wales.
Conclusion
In conclusion, lifting inspections in South Wales are an essential component of workplace safety and compliance. By adhering to regulations, conducting regular inspections, and choosing the right service provider, businesses can protect their employees and enhance operational efficiency. With Safe Plant UK’s expertise and commitment to safety, you can ensure your lifting equipment is up to standard, giving you peace of mind and allowing you to focus on growing your business.
lifting inspections south wales