Understanding GRP Feeder Pillars: The Future of Electrical Distribution
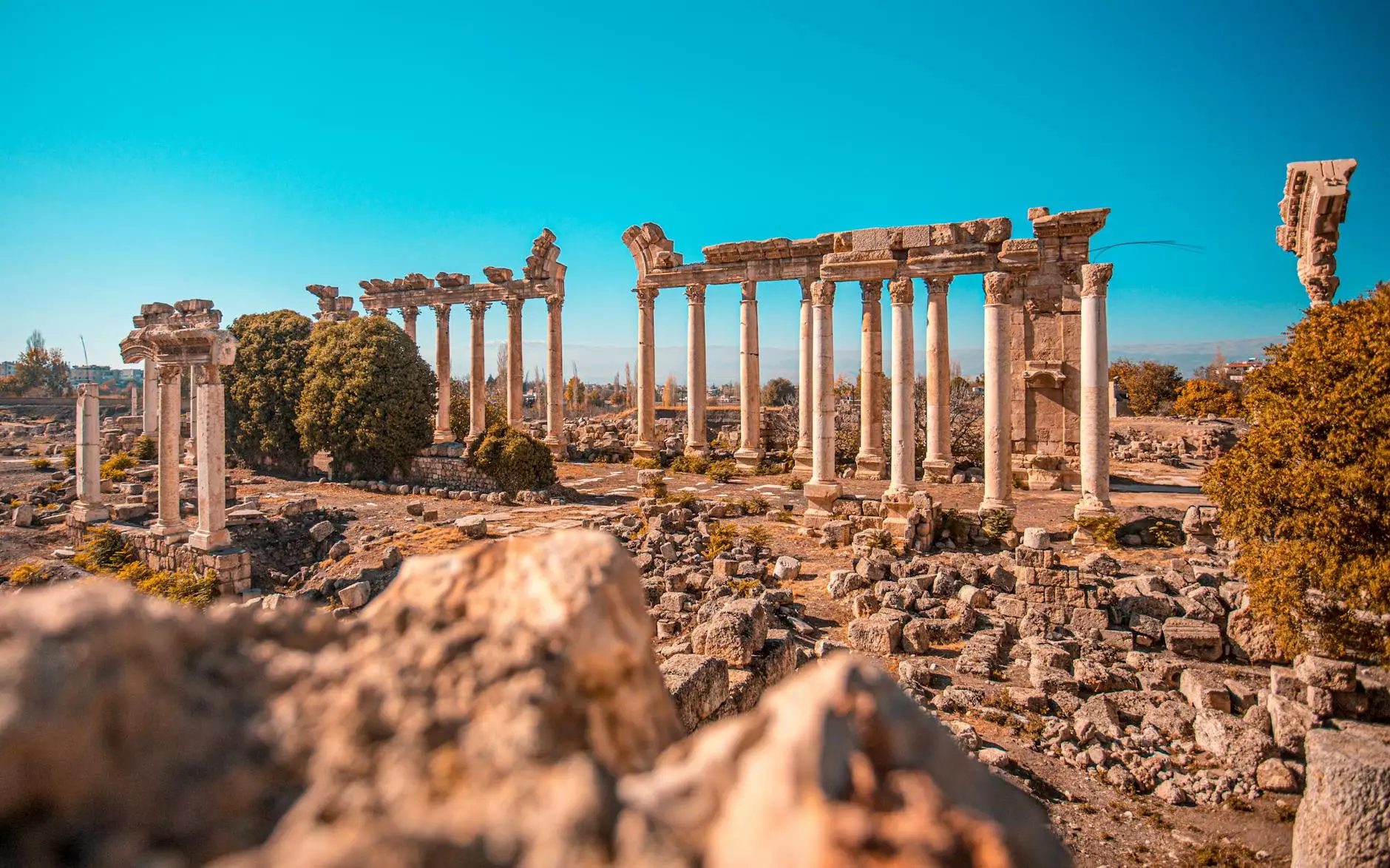
GRP feeder pillars are emerging as a prominent solution in the realm of electrical distribution systems, revolutionizing how power is distributed in various industrial and commercial applications. Incorporating innovation and sustainability, these feeder pillars present many benefits, making them ideal for use in contemporary projects. In this comprehensive article, we will delve into the intricacies of GRP (Glass Reinforced Plastic) feeder pillars, emphasizing their significance in the electrical engineering and construction industries.
What Are GRP Feeder Pillars?
GRP feeder pillars serve as enclosures for electrical distribution, acting as a crucial link in the network that distributes electricity efficiently from a central power source to individual consumer units. Made predominantly from glass reinforced plastic, these feeder pillars are designed to withstand the rigorous demands of outdoor environments while offering significant advantages over traditional materials such as metal.
Key Characteristics of GRP Feeder Pillars
- Corrosion Resistance: GRP materials do not rust or corrode, ensuring longevity and reducing maintenance costs.
- Lightweight: Unlike metal alternatives, GRP feeder pillars are significantly lighter, facilitating easy installation and transportation.
- Electrical Insulation: GRP provides excellent electrical insulation, enhancing safety during operation and installation.
- Customization: These feeder pillars can be custom-made to meet specific dimensions and requirements of projects.
Applications of GRP Feeder Pillars
Due to their robust properties, GRP feeder pillars find extensive application across various sectors:
1. Residential Developments
In residential areas, GRP feeder pillars help manage the distribution of electricity to homes efficiently. Their lightweight nature ensures quick installation, making them ideal for new housing developments.
2. Commercial Facilities
Businesses rely on efficient electrical distribution systems. GRP feeder pillars play a crucial role in commercial buildings, ensuring reliable power supply to different operational sections within the facility.
3. Infrastructure Projects
Public infrastructure projects, such as street lighting and traffic management, benefit significantly from GRP feeder pillars due to their durability and resistance to harsh weather conditions.
4. Renewable Energy Systems
As the renewable energy sector grows, so does the need for efficient electrical distribution systems. GRP feeder pillars can effectively manage connections from solar panels and wind turbines to the grid.
Advantages of Using GRP Feeder Pillars
Choosing GRP feeder pillars for electrical distribution systems offers numerous advantages that contribute to their rising popularity:
1. Durability and Longevity
Constructed from high-quality synthetic materials, GRP feeder pillars exhibit exceptional durability. They can withstand extreme weather conditions, including heavy rain, snow, and intense sunlight, ensuring they remain reliable over time.
2. Cost-Effectiveness
The lightweight nature of GRP feeder pillars translates into lower installation costs and reduced labor efforts. Furthermore, their resistance to corrosion means that long-term maintenance costs are significantly minimized, providing value for money in the long run.
3. Flexibility in Design
GRP feeder pillars can easily be manufactured to meet specific project needs, whether it be size, shape, or functionality. This flexibility allows engineers and constructors to design systems that prioritize efficiency and performance without compromising aesthetics.
4. Environmental Considerations
With an increasing focus on sustainability, choosing GRP materials aligns with environmental objectives. Their longevity and reduced need for replacement contribute to lower waste production in the long term.
Comparative Analysis: GRP vs. Traditional Materials
When considering materials for feeder pillars, it's essential to compare GRP with traditional options like steel and concrete. Here’s how they stack up:
1. Weight
- GRP: Lightweight and easy to handle, facilitating straightforward installation.
- Steel/Concrete: Heavier and often requires additional resources for transport and installation.
2. Maintenance
- GRP: Minimal maintenance due to corrosion resistance and durability.
- Steel/Concrete: Requires regular maintenance and is susceptible to corrosion and degradation over time.
3. Insulation
- GRP: Excellent electrical insulation properties, enhancing safety.
- Steel: Conductive and requires additional insulation protection.
4. Aesthetic Appeal
- GRP: Can be manufactured in various colors and finishes, contributing to aesthetic integration in the environment.
- Steel/Concrete: Generally utilitarian and less visually appealing.
Installation Considerations for GRP Feeder Pillars
Proper installation is vital for the effective performance of GRP feeder pillars. Here are important factors to consider:
1. Site Assessment
Before installation, conduct a thorough site assessment to evaluate soil conditions, potential hazards, and layout plans. Understanding the environment ensures that the feeder pillar is positioned optimally.
2. Compliance with Regulations
Ensure that the installation of GRP feeder pillars complies with local regulations and electrical codes. This adherence guarantees safety and operational efficacy.
3. Professional Installation
While GRP feeder pillars are easier to install than traditional materials, hiring qualified professionals is crucial to ensure that all aspects are handled expertly, minimizing risks of future issues.
Conclusion: Embracing the Future with GRP Feeder Pillars
As industries evolve towards more efficient and sustainable solutions, GRP feeder pillars represent a transformative shift in the electrical distribution sector. Their unique characteristics provide unmatched benefits such as durability, cost-effectiveness, and environmental sustainability. By embracing GRP technology, businesses and communities can enhance their electrical systems' reliability and efficiency, ensuring progress towards a more sustainable future.
For more information on how to incorporate GRP feeder pillars in your projects, contact the experts at Celtic Composites, where innovative solutions meet industry demands.